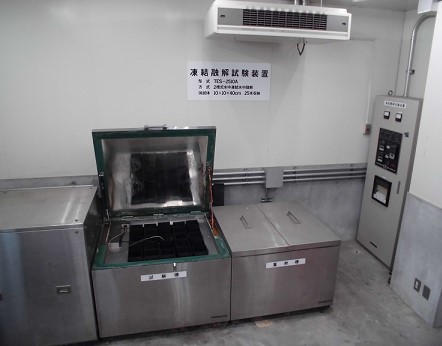
コンクリートは、凍害、塩害、中性化、アルカリ骨材反応、化学的浸食など様々な要因で劣化します。
コンクリート構造物が、長期の耐久性を持つためには、これらの劣化要因を良く知る必要があります。
今回は、コンクリート構造物の耐久性に影響を及ぼす劣化要因と、その劣化要因の試験について簡単にご紹介したいと思います。
この記事でわかること
コンクリート構造の耐久性とは
コンクリート構造の耐久性とは、気象作用、物理的摩耗作用、化学的浸食作用、その他の劣化作用などに抵抗し、構造に要求される性能を長期間にわたって発揮する能力のことをいいます。
コンクリートに作用する劣化について
コンクリートに作用する劣化は、通常、複数の劣化の複合で進行することが多いです。
また劣化には、化学的なものと物理的なものがあります。
化学的なもの・・・塩害、中性化、化学的侵食、アルカリシリカ反応など
物理的なもの・・・すり減り作用など
また劣化について理解するうえで、下記の2点を知っておくことが肝心です。
①コンクリートは、長期にわたりセメントの水和反応による化学反応が進行します。
その反応のプロセスと反応生成物は、コンクリート中の化学物質の種類・量、外部からの化学物質の種類・量、環境条件などの影響を受けます。
②コンクリートは、連続した微細な空隙を有する多孔質物質です。
この空隙を通って、酸素、二酸化炭素などの気体、塩化物イオン、アルカリ金属イオン、硫酸イオンなどのイオン、水分などの浸透や移動が生じます。
塩害
塩害は、コンクリート中にある塩化物イオンにより鉄筋が腐食し、コンクリート構造の性能を低下させることを言います。
コンクリートは、アルカリ性で、鉄筋の表面に腐食抑制作用のある不動態被膜が生じるので、鉄筋は錆びにくい状態にあります。
不動態被膜は、鉄の酸化物、オキシ水酸化物でできています。
コンクリート中に塩化物イオンが、一定量以上あると、不動態被膜が破壊され、鉄筋が錆びやすくなります。
コンクリートに塩化物イオンが侵入する原因としては、下記の2点があげられます。
①内在塩化物イオン
海砂、混和剤、セメント、練り混ぜ水など最初から含まれているもの
②外来塩化物イオン
海水飛沫、飛来塩化物、凍結防止剤などの塩化物がコンクリート表面から浸透するもの
また海岸から離れていても、河川や地下水に海水濃度近くの塩分が含まれている場合には、塩化物イオンが供給されることもあります。
不動態被膜が破壊されると、塩化物やアルカリ濃度の差などの不均一性のために、鉄筋の表面の電流が流れ、鉄筋に錆び(腐食)が生じます。
これは鉄筋の表面にアノード部(陽極)とカソード部(陰極)が生じ、鉄筋の表面に電位差が生じることにより電流が流れるのです。
鉄筋の錆びは、元の体積の2~3倍にもなり、その膨張圧により鉄筋に沿ってコンクリートにひび割れが生じます。
ひび割れも生じると、酸素と水の侵入し、さらに錆が進み、コンクリートの剥落や鉄筋の断面積の減少による部材耐力の低下に至ります。
塩害による劣化の進行過程は、鉄筋の錆が発生する前が潜伏期、錆が発生すると進展期、コンクリートにひび割れが生じると加速期、部材耐力の低下が生じ始めると劣化期というように4段階で評価されています。
塩害に影響する要因としては、水セメント比、セメントの種類などがあげられ、密実なコンクリートほど塩害の進行は遅くなります。
≪対策≫
鉄筋の錆は、水と酸素が供給塩化物イオンが存在する場合に進行します。
鉄筋の錆を防ぐには下記の6点が有効となります。
①コンクリート中の錆の原因物質を除去する。
②コンクリートへの錆の原因物質の侵入・浸透を抑制する。
③鉄筋表面への錆の原因物質の到達を抑制する。
④防食性の鉄筋を使用する。
⑤鉄筋の電位を制御する。
⑥防錆剤を使用する。
土木学会コンクリート標準示方書では、塩化物イオンの侵入に伴う鉄筋腐食に関する確認として、構造物の設計耐用年数における鉄筋位置での塩化物イオン濃度が鉄筋腐食発生限界濃度以下であることを確認することになっています。
ただし、外部からの塩化物の影響を受けない環境条件の場合には、コンクリートの練り混ぜ時に、コンクリート中に含まれる塩化物イオン脳の総量が0.3kg/m3以下であれば、塩化物イオンによる構造物の構造性能は失われないとしています。
日本建築学会JASS5では、塩化物イオン総量を0.3kg/m3に規制しており、防錆上有効な対策を行った場合は0.6kg/m3まで許容しています。また最も影響が大きい海砂については、塩化物許容値を0.04%(NaClとして)としています。
レディーミクストコンクリート(JIS A 5308)においても同様の規制を設けています。
塩化物イオン量の規制値0.3kg/m3を、例えば、塩化ナトリウム(NaCl)に換算すると、約0.5kg/m3に相当することになります。
ナトリウム(Na)と塩素(Cl)の原子量は、それぞれ23と35.5
0.3kg/m3 ×(23+35.5)/ 35.5 = 0.49 kg/m3
コンクリート用化学混和剤のJISにおいては、混和剤中に含まれる塩化物の量を3種類の区分に設けていますが、ほとんどが1種になります。
1種 塩化物イオン量 0.02kg/m3以下
2種 塩化物イオン量 0.02kg/m3を超え、0.20kg/m3以下
3種 塩化物イオン量 0.20kg/m3を超え、0.60kg/m3以下
コンクリートを密実にするためには、水セメント比をできるだけ小さくし、コンクリートを締固めるように入念に施工を行います。
また高炉スラグ微粉末などの混和材を使用することも防食上の効果があります。
≪塩化物含有量の試験≫
フレッシュコンクリート中(固まっていないコンクリート)の塩化物量は、液相中に含まれる塩化物イオン濃度を測定し、これに単位数量をかけて求めます。
工事現場で、フレッシュコンクリート中の塩化物量を測定する簡易測定方法としては、
3つの方法があります。
①試験紙法 ②イオン電極法 ③電極電流測定法
測定法は、原理、精度、特性等を十分理解した上で、信頼できる機関で評価を受けた試験方法を選択し、同じ測定法を継続して行うことが良いです。
硬化コンクリートの測定には、試料を粉末にし、酸で溶かして、塩化物を抽出し、その溶液中の塩化物イオン濃度を測定し、総塩化物量に換算する方法があります。
硬化コンクリート中に含まれる塩化物イオン試験方法は、JIS S 1154 に記載されており、日本コンクリート工学会の「硬化コンクリート中に含まれる塩分の分析方法」をベースに制定されました。
中性化
中性化は、空気中の二酸化炭素の作用を受けて、コンクリート中の水酸化カルシウムが炭酸カルシウムになり、コンクリートのアルカリ性が低下することをいいます。
Ca(OH)2 + CO2 → CaCO3 + H2O
コンクリートのアルカリ性が低下すると、鉄筋の不導態被膜が破壊されやすく、水や酸素の浸透により鉄筋が錆び、構造物の耐久性が低下します。
影響する要因としては、水セメント比、セメントと骨材の種類、混和材料などがあげられます。また密実なコンクリートほど中性化の進行は遅くなります。
中性化の進行は、時間の平方根に比例されます。
x=b × √(t)
x:中性化速さ b:中性化速度係数 t:時間
中性化が進むとコンクリート中の固定化された塩化物イオン(フリーデル氏塩)が遊離し、コンクリート内部へ移動して塩化物イオン濃度が濃縮されます。
中性化速度は、二酸化炭素濃度が高いほど、湿度が低いほど、温度が高いほど早くなります。大気中の相対湿度が40~60%程度の際に、中性化速度は最大値を示しますが、極端に乾燥している場合や、濡れている場合には中性化は、進みにくい傾向にあります。
≪対策≫
対策としては、下記の2つに分けることができます。
①中性化の進行を抑制する。
②鉄筋の腐食の進行を抑制する。
中性化の進行を遅らせる方法としては、タイルなどの仕上げ材を張ったり、鉄筋のかぶり厚さを大きくしたり、気密性の吹き付け材を行ったりすることなどがあります。
また中性化したコンクリートにアルカリを電気浸透させることにより、コンクリートの低下したpHを上昇さえる再アルカリ化工法も開発されたりしています。
≪中性化試験≫
コンクリートの中性化深さの測定方法は、JIS A 1152 に記載されています。
フェノールフタレイン1%のエタノール溶液を、構造物から採取したコンクリートに噴霧して調べます。中性化していない部分は赤紫に着色し、中性化部分は着色しません。
構造物の外側から鉄筋表面まで、無着色部分がどのくらいまで進行しているかで、判断しますが、実際は、鉄筋が錆びるのは、無着色部分に到達する前に発錆します。
コンクリートの促進中性化試験方法が、JIS A 1153 に定められており、コンクリートの種類や使用材料等が異なる場合の中性化深さを相対的に比較することができます。
アルカリシリカ反応
アルカリシリカ反応は、一般にASRと言われています。
この反応は、コンクリート中の水酸化アルカリと骨材中のアルカリ反応性鉱物との化学反応で、アルカリシリカゲルという反応生成物を作ります。
このアルカリシリカゲルが吸収膨張して、コンクリートに悪さを起こし、ひび割れを起こします。
この反応が進むと、ひび割れが生じ、ゲルがにじみでたり、目地のずれなどが生じたりします。
このひび割れの入り方には特徴があり、無筋コンクリート構造の場合は、亀甲状のひび割れが生じます。また鉄筋コンクリート構造の場合は、主筋方向にひび割れが生じます。
これは、拘束されている方向と直交方向に生じるからです。
アルカリシリカ反応によるひび割れは、部材耐力が急激に低下することは、少ないと考えられています。これは、ひび割れが部材内部まで達していないことが多いためです。しかし近年、このアルカリシリカ反応による膨張力により、伸び能力の低い鉄筋の曲げ部や、圧接部で鉄筋が破断することが報告されているので注意が必要です。
また塩化物イオンや酸などの劣化因子の侵入や凍害に対する抵抗性が低下するため、鉄筋が腐食する可能性が増えることが分かっています。
このアルカリシリカ反応は、下記の3条件が揃うことで生じます。
①反応性鉱物を含む骨材が一定以上存在する。
②細孔溶液中に十分な水酸化アルカリが存在する。
③コンクリートが多湿、湿潤状態の場所。
反応性鉱物は、火山ガラス、クリストバライト、トリディマイト、オパールカルセドニー、隠微晶質石英などがあります。
アルカリシリカ反応は、反応性骨材の量が多いほど、膨張が大きくなるわけではありません。膨張が最も大きくなるのには、骨材中に含まれる反応性骨材の割合があります。
この割合のことをペシマム量と言います。
この量は、セメント中のアルカリ量、骨材の種類、粒度などによって変化します。
反応性骨材量と膨張量との関係をペシマム曲線と言います。
コンクリート中のアルカリの主な供給源は、セメントになります。セメント原料の粘土鉱物などからNa2OやK2Oが供給されます。
単位セメント量が多すぎたコンクリートは、アルカリ骨材反応の抑制に不利になります。 セメント中のアルカリ量はセメントの製造工場によっても異なってきます。
アルカリの供給源は、セメント以外にも、海砂に付着した塩化物や、コンクリート硬化後に外部から侵入する塩化物、凍結防止剤、混和剤などがあります。さらにコンクリート中の水分の移動によってアルカリ濃度が凝縮される現象もあるといわれています。
アルカリ骨材反応の膨張には、多湿、湿潤状態の場所とあるように、水分が必要であり、雨の影響を受けやすい打ち放しコンクリートや、内部の水分が乾燥し難い大きい部材に損傷が生じやすくなります。
≪対策≫
アルカリシリカ反応を抑制する方法として、3つの方法がある。
①コンクリート中のアルカリ総量を規制する方法
②アルカリシリカ反応抑制効果のある混合セメントを使用する方法
③安全と認められる骨材を使用する方法
①コンクリート中のアルカリ総量を規制する方法
全アルカリ量が明白なポルトランドセメントを使用し、アルカリ総量が、3.0kg/m3以下になるよるようにする。
総量とは、セメント、混和材、骨材、混和剤、流動化剤のそれぞれの全アルカリ量を足したものになります。
詳しくは、JIS A 5308を見てみてください。
②アルカリシリカ反応抑制効果のある混合セメントを使用する方法
抑制効果のある混合セメントは、下記の適合したものを用います。
・JIS R 5211 に適合する高炉セメントB種 または C種
ただし、高炉セメントB種の高炉スラグの分量は、質量比で40%以上
・JIS R 5213に適合するフライアッシュセメント B種 または C種
ただし、フライアッシュセメントB種のフライアッシュの分量は、質量比で15%以上
高炉スラグ微粉末またはフライアッシュを混和剤として使用する場合には、一緒に使用するポルトランドセメントとの組み合わせにおいて、アルカリシリカ反応抑制効果があると確認された単位量にて使用します。
③安全と認められる骨材を使用する方法
アルカリシリカ反応試験において、化学法またはモルタルバー法の試験結果が、「無害」と判定されてものを使用します。
海水や潮風を受ける地域の建物、凍結防止剤の塩化ナトリウム(NaCl)の影響を受ける建物には、塩化物の浸透を防止するための防水仕上げを施すことも有効になります。
またコンクリート中への水分の浸透を防止するために防水塗装することも有効になります。ただし、気を付けなくてはならないのは、湿潤状態にある建物に対して、防水塗装などの表面被覆を行うと、内部の水分がコンクリート中から抜けなくなり、返ってアルカリシリカ反応が進行することがあります。
アルカリシリカ反応以外の骨材による劣化
アルカリシリカ反応を起こす骨材以外に、コンクリートにひび割れやポップアウトなどの損傷を起こす鉱物類があります。
具体的には、下記のようなものがあります。
①モンモリロナイト
吸収すると膨張し、乾燥すると収縮するため、ひび割れやポップアウトが生じやすいです。ただ一般的には、フレッシュコンクリートの異常凝結促進の影響が問題となっています。
②ローモンタイト
乾湿の繰り返しにより体積変化を生じ、粉状になりやすいため、骨材中に少し含まれていたとしてもコンクリート表面の剥離やポップアウトが生じます。
③含鉄ブルーサイト
含鉄ブルーサイトを含む骨材が、コンクリート表面近くにあると、酸化しやすく、膨張を起こし、ポップアウトが生じます。
④黄鉄鉱
黄鉄鉱を含む骨材が、コンクリート表面近くにあると、酸化分解してコンクリート表面に褐色の錆汁と出したり、石こうやエトリンガイトを生成して膨張し、コンクリートにひび割れやポップアウトを生じさせるものがあります。
≪対策≫
アルカリシリカ反応以外の有害鉱物が含まれているかどうかの判定には、粉末X線解析や偏光顕微鏡観察が主に用いられます。
有害鉱物の許容量は、骨材中の存在状態やコンクリートの配合、使用環境条件ともに密接に関係があり、現状では明確ではありません。
おおよその目安は考えられていますが、有害鉱物を含むものを使用しないことが得策です。
化学的浸食・溶脱
外部の環境からの化学物質とコンクリートの化学反応によって生じる劣化は、主に3種類に分けることができます。
①コンクリート中のセメント水和物との化学反応により、水に溶けにくしセメント水和物を可溶性物質に変化させます。これによりコンクリートの組織が多孔質化したり、分解したりして劣化が生じます。
劣化因子の例は、下記のものがあります。
酸、動植物油、無機塩類、腐食性ガス、炭酸ガス、硫酸の生成を伴う微生物の作用など
②コンクリート中のセメント水和物との化学反応により、新しく膨張性化合物を生成します。この時の膨張圧により劣化が生じます。
劣化因子の例は、下記のものがあります。
動植物油、硫酸塩、海水、アルカリ濃厚溶液など
③コンクリートが長い間、水に接することにより、セメント水和物の成分が外部に溶脱します。これにより硬化体組織が多孔化し劣化が生じます。
硫酸や塩酸などの強酸は、セメント水和物を分解させて、コンクリートが劣化します。
酢酸その他の有機酸の分解作用は、強酸に比べて弱いです。ただ基本的には、コンクリートは酸に対する抵抗性が低いです。
硫酸塩は、水酸化カルシウム、アルミン酸三カルシウムと反応してエトリンガイトを生成します。これにより著しく膨張が生じコンクリートを破壊に至らせます。
海水に含まれる硫酸マグネシウムは、硫酸塩と同じ劣化をもたらせます。また塩化マグネシウムは、コンクリート中の石灰と化合してコンクリートを水溶性にし劣化します。
下水に含まれる硫酸塩は、微生物の作用で硫化水素から硫酸となります。これは管路や下水処理場のコンクリートに劣化を生じさせます。
大気中の窒素酸化物や硫黄酸化物が原因の酸性雨(pH5.6以下)により、コンクリートに劣化を生じさせることもあります。
ショ糖、果糖、糖蜜などの糖類の水溶液は、コンクリート中の水酸化カルシウムと反応して可溶性の糖酸カルシウムを生成します。これが溶出し組織を多孔化して劣化します。
動植物油による影響は、脂肪酸の構成割合のほかに粘性も影響します。粘性が低くコンクリートに浸透しやすいものほど劣化は激しくなります。コンクリートが膨潤しひび割れが生じて表面が剥離することが多いです。
コンクリート中のカルシウム成分が、地下水や海水など周囲の水によって溶解します。これにより水和組織が疎となり多孔化します。この現象をカルシウム成分の溶脱といいます。ただ溶脱による劣化は、進行が非常に緩やかなため、使用期間中における力学特性が低下することは少ないです。
セメント硬化体中の可溶性成分を溶解した水が表面に、にじみでてきて、水の蒸発によって溶けた成分が表面にでてきたりします。この現象をエフロレッセンスと言います。
可溶性成分には、カルシウムイオン、アルカリ金属イオン、硫酸イオンがあります。
この現象には、次の場合に生じたりします。
①硬化がまだ十分でない場合
②水セメント比が大きい場合
③施工不良の目地があるときで、透水しやすいコンクリートの場合
また水洗いしていない海砂を使用したときに塩類が析出したりすることがもあります。
≪対策≫
化学的侵食は、使用条件等の影響があるため、設計時に耐用年数を考慮し、十分な対策をとったり、定期的な補修計画を行い、最初から計画をしておくことが重要になります。
酸や硫酸塩に関しては、コンクリート表面に被覆を施すだけで、効果的です。
海水作用に関しては、耐硫酸塩ボルトランドセメント、中庸熱ポルトランドセメント、高炉セメント、フライアッシュセメントを使用することも比較的抵抗性があり有効です。
塩害に対する対策と同様に、海水以外の侵食作用に対しても、かぶり厚さを十分確保するなどして、鉄筋を錆びないように保護し、水セメント比の小さい水密性の高いコンクリートを作ることも有効になります。そのため十分な締め固めと養生を行うことが重要です。
下水施設などにおける劣化対策に関しては、抗菌剤を混和剤として使用することも有効になります。
セメント水和物の溶脱に関しては、現状では、具体的な対策が確立されていないていません。
凍害
寒い地方では、コンクリート中の水分が凍結します。
この時、水の凍結膨張に見合う水分がコンクリート中を移動し、その際の水圧がコンクリートを破壊させます。この破壊はセメントペーストの中、骨材の中、セメントペーストと骨材の境界面で生じたりします。
また水の凍結膨張は、体積膨張率が約9%にもなります。
耐凍害性に対して低い骨材を使用すると、骨材自体が割れ、コンクリートを劣化させます。
また吸収率の高い軟石を使用した場合は、骨材自体が凍結時に膨張し、表面のモルタルをはじき出すことがあります。これをポップアウトといいます。
コンクリートとしての耐凍害性は、空気量に関係してきます。
空気量が同じ場合、微小で独立した気泡が入っているほど、耐凍害性は良くなります。
これは気泡間隔係数というもので表され、小さいほど良いということになります。
凍結融解作用を受けて劣化しますが、これは凍結と融解の繰り返し作用により生じます。つまり日が当たらないで、水が溶けない部分よりも、日が当たり凍結誘拐を繰り返す部分の方が、劣化が大きくなります。
海水の作用と、凍結融解の作用が合わさった場合、劣化作用はさらに大きくなります。
北海道、東北、北陸などの海岸地域のコンクリートには、スケーリングやひび割れが、見られることが多いです。
さらに凍結防止剤が散布される部分には、劣化が促進される場合があります。
また凍結によりコンクリート中の塩分は、コンクリート内部へ移動し、鉄筋部分で塩分濃度が高くなり、塩害が生じることになります。
≪対策≫
対策としては、耐凍害性のある大きな骨材を使用します。この骨材の判定には、硫酸ナトリウムによる骨材の安定性試験方法(JIS A 1122)があります。
耐凍害性をあげる重要な要素としては、AE剤、AE減水剤、高性能AE減水剤を用いて、使用環境条件として、粗骨材の最大寸法等に応じ、3~6%の適正量のエントレインドエアを連行させることです。このエントレイドエアは、コンクリートの硬化後も水に満たされることはない 小さな空気の泡で、凍結時に水の逃げ道になると考えられています。
気泡間隔係数等の気泡の特性が同じ場合には、水セメント比を少なくして、密実なコンクリートとすることで、耐凍害性を高めることもできます。
水切り、水勾配、防水等を工夫することで、融雪水がコンクリートにしみ込まないようにすることも効果的です。
すり減り
すり減り作用には、下記の2種類があります。
①車両などによるすり磨き作用
②海水中の砂などによる突き砕き作用
最初は、表面に近いモルタル部分で生じます。その後、内部の荒い砂や粗骨材が露出します。骨材はすり減り抵抗性に大きく影響します。
キャビテーションによる空洞は、水流のため押しつぶされ高圧を生じます。このときの負圧、高圧の繰り返しにより損傷を受けます。
キャビテーションとは、高速の水流にさらされる部材の表面の凹凸の部分や屈曲した部分に、水が跳躍して表面から離れる際に、負圧の空洞を生じる現象です。
≪対策≫
対策としては、下記の3点があげられいます。
①水セメント比を小さくして、圧縮強度を大きくする。
②キャビテーションに対して、平滑な表面にする。
③すり減り抵抗性の高い骨材を使用する。
電流の作用による劣化
鉄筋コンクリートは、鉄筋からコンクリートに向かって電流が流れると、鉄筋が酸化して腐食する電食という現象が生じます。コンクリートに塩化カルシウムなどの塩化物を含む時が、その影響が大きくなります。
コンクリートから鉄筋に向かって過大な電流が流れると、コンクリートが弱くなり付着強度が低下します。また鉄筋の表面および内部には、水素を発生させます。
PC鋼材などでは、水素脆化が生じることが知られています。
ただし、コンクリートから鉄筋に向かって電流を流すことは、鉄筋の電気防食工法、脱塩工法、再アルカリ工法、電着工法の原理でもあり、電流量が適正であれば、付着強度の低下や水素脆化の心配はありません。
鉄筋からコンクリートに向かって電流が流れると、鉄筋は陽極となります。
またコンクリートから鉄筋に向かって電流が流れると、鉄筋は陰極となります。
コンクリートが乾燥していると電流は流れにくくなり、電食も少なくなります。
無筋コンクリートの場合は、直流および交流による被害は、受けません。
コンクリートの耐久性に関する試験
凍結融解試験
コンクリートの耐凍害性試験は、凍結融解作用を人工的に行います。
凍結融解作用を所定の回数繰り返す試験を行い、耐久性指数(相対動弾性係数の保持の度合い)により評価します。
凍結融解試験方法(JIS A 1148)に定める水中凍結融解試験方法(A法)に基づいて、100×100×400mmのコンクリート供試体を作製し、凍結融解作用を300回繰り返して行います。
その際、耐久性指数が所定の値以上であれば、合格とします。
塩分浸透試験
塩化物イオンの拡散係数試験には、下記の2つの方法があります。
①浸漬法による見掛けの拡散係数
②電気泳動法による実効拡散係数試験方法
促進中性化試験
促進中性化試験は、CO2濃度5%環境下において、強制的にコンクリートを中性化させます。
その後、フェノールフタレインを塗布して、中性化深さを測定します。
アルカリシリカ反応性試験
試験方法は、化学法とモルタルバー法などがあります。
化学法は、アルカリに対する骨材の潜在的な反応性を科学的に試験するものです。
モルタルバー法は、モルタルの長さ変化を測定することにより骨材の潜在的な反応性を試験します。
この化学法またはモルタルバー法で骨材の試験を行い、「無害」(区分A)と「無害でない」(区分B)に区分することにしています。
化学法・・・・骨材のアルカリシリカ反応性試験方法(JIS A 1145)
粉砕した骨材を80℃のアルカリ溶液で反応させ、アルカリ濃度減少量Rcと溶解シリカ量Scから骨材の反応性を判定します。
骨材のアルカリシリカ反応性の判定は、Sc >10mmol/ℓ かつ Rc < 700mmol/ℓ のとき Rc ≦ Sc を「無害でない」とし、それ以外を「無害」とします。
モルタルバー法・・・骨材のアルカリシリカ反応性試験方法(JIS A 1146)
粒度調整を行った試料を用いて、水セメント比が50%、水酸化ナトリウムの添加によりセメントのアルカリ量を1.2%に調整したモルタルバーを作製する。モルタルバーの大きさは、40mm×40mm×160mmとする。
モルタルバーを温度40±2℃、相対湿度95%以上の条件下に6カ月間保存したときの膨張量が0.1%以上の骨材を「無害でない」とし、それ以外を「無害」とします。
2種類以上の骨材を混合して使用する場合には、化学法では、それぞれの骨材を試験し、1つでも「無害でない」と判定された場合には、混合した骨材は、「無害でない」として扱います。またモルタルバー法では、実際に使用する比率で混合した骨材で試験を行い、ペシマム量の判定を行う場合もあります。
このほかにも、コンクリートでの反応性試験が、日本コンクリート学会、日本建築学会で定められいますが、それぞれに特徴と課題があります。
まとめ
コンクリートの耐久性試験に関しては、劣化要因を良く知り耐久性試験を行ってください。